Table of Contents
What is Pipe Extrusion?
A pipeline produces process is material preparation→mixing material→feeding material→thermoplastic→extrusion→forming → cutting. Extrusion is a process that involves creating objects of fixed cross-sectional profiles. The process is used for different types of materials that include ceramics, modeling clay, concrete, foodstuffs, polymers, and metals.
Also, the process creates various shapes to become useful for different applications. You can also consider custom plastic extrusion. The process will combine advanced properties to create a product that can meet some specific needs.
The plastic pipe extrusion process that includes the PVC extrusion process starts with plastic material feeding on hoppers into the extruders’ barrel. Mechanical energy is used to melt the material. There will be a few steps in the extrusion process.
Every step is essential to decide the final characteristics of the product. The extrusion method relies on specific factors such as quality control and experience to develop a consistent factor. Some determining factors in the extrusion process are force, tension, speed, temperature, and time.
Typical Extrusion Materials
A wide variety of materials are used in the extrusion process. Here we can take the example of the PVC extrusion process. Some other materials are polyethylene, acetal, nylon, acrylic, polypropylene, polystyrene, polycarbonate, and acrylonitrile. These are the primary materials used in the extrusion process. However, the process is not limited to these materials.
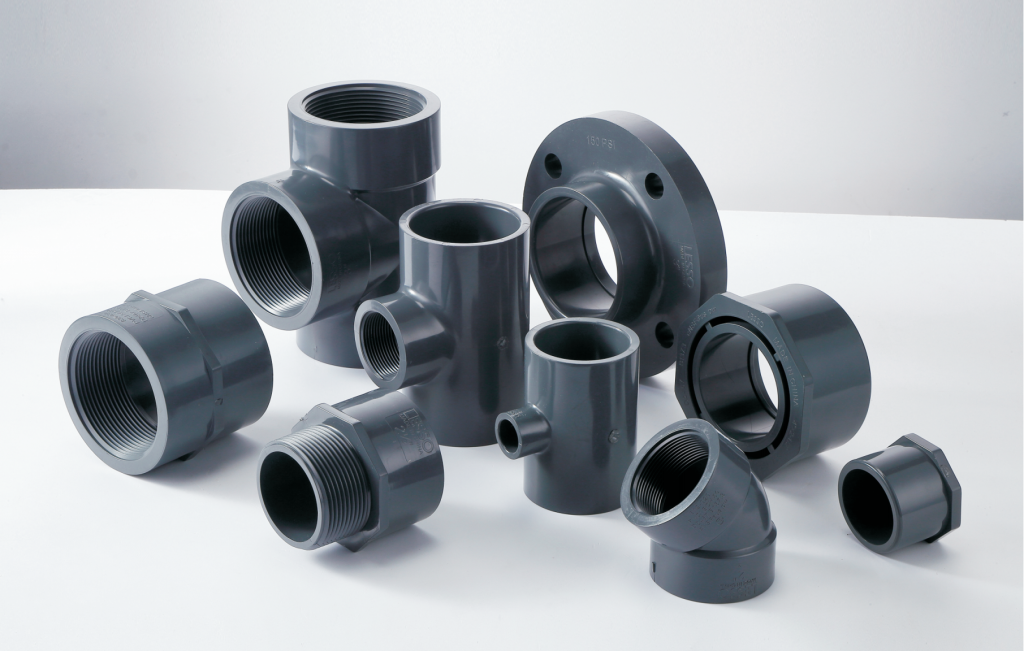
Plastic Extrusion Process Basics
The plastic extrusion process will start with the raw resin replacement. First, it will be placed in the hopper of the extruder. When the resin will not have additives for some specific application, additives will be added to it in the hopper. After placing them, the resin will be fed by the hopper’s feed throat, and then it will go to the barrel of the extruder. There is a rotating screw in the barrel. That will feed the resin, and the resin will move along within the long barrel.
During the process, the resin will be exposed to high temperatures. The extreme temperature will melt the material. The temperature might vary between 400 and 530 degrees F based on the barrel temperature and type of the thermoplastic. Also, many extruders will have a barrel that can increase the heat gradually starting from the loading to feeding to melting. The entire process reduces the risk of plastic degradation.
The plastic will melt and reach the barrel end, and then it will be forced by a screen pack to the feed pipe, and ultimately, it will die. In the extrusion process, the screen will play the role to eliminate contaminants from the molten plastic. The number of screens, the porosity of screens, and a few other things will be manipulated to ensure uniform melting. Also, the backpressure helps in uniform melting.
Once the melt material reaches the feed pipe, it will be fed into the die hollow. Finally, it will cool down and harden to create the end product. The newly made plastic gets a sealed water bath to speed up the cooling process. However, the water bath will be replaced by cooling rolls during sheeting extrusion.
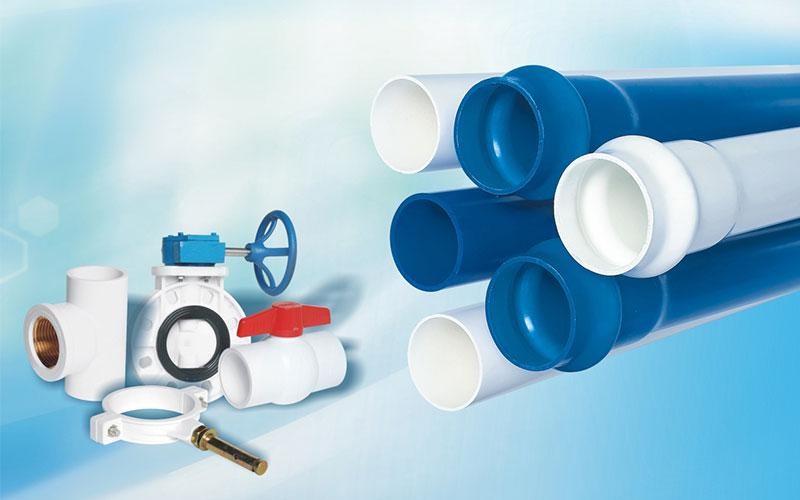
The Major Steps in Plastic Pipe Extrusion Process
As stated earlier, the plastic extrusion process creates a wide range of products ranging from building materials to industrial parts, electrical covers, window frames, edging, weather stripping, and fence. However, the process of making all these different products will be the same with a minimal difference. The method of the plastic pipe intrusion involves the following.
Material Melting
The raw materials that include pellets, powder, or granules will be loaded into the hopper. After this, the materials will be fed into the heated chamber known as the extruder. The materials will melt while moving through the extruder. Extruders will have either two or one spinning bolt.
Material Filtration
After melting the materials, the filtration process will start. The melted material will flow from the hopper through the feed throat to the spinning screw that operates within the extrusion machine. The spinning screw works in the horizontal barrel, and within that barrel, the melted material will be filtered to get a uniform consistency.
Sizing the Molten Material
The plastic material properties will vary based on the raw materials used in the process. However, all the raw materials will be processed with heat. The materials will be exposed to extreme heat at a particular temperature. The temperature level will vary according to the raw material. During the process completion, the molten plastic will be pushed by an opening that is called a die. It will enable the material to be shaped to the end product.
Workup Process
In this step, the die-cut for the profiles will be designed to have an even and smooth flow from the extruder’s cylindrical profile into the last profile shape. It is worth mentioning that consistency is crucial in the plastic flow to get reliable and high-quality products.
Material Cooling
The plastic will be extruded from the die, and then it will be fed onto a belt for cooling. The belt is called a conveyor belt. After going through this step, the final product will be cooled by water or air. It is worth mentioning that the process will be similar to injection molding. But the difference is that the melted plastic will be forced by a die. But in the injection molding, the process will go through the mold.
Summary
The plastic pipe extrusion goes through a complex process to create the final product. The process manufactures a wide range of products. You can also choose custom plastic extrusion to find a product based on your specific needs. Plastic extrusion products are used in many applications such as filtration, military, automotive, industrial, and medical industries.
However, you will need the best products to ensure a durable result. If you want the best PVC pipes, you can consider visiting LESSO’s PVC pipes. LESSO has a good reputation for manufacturing different types of PVC pipes. You can check the features to know which one can meet your specific needs. There are many options for both commercial and residential usages.
Recommend Reading
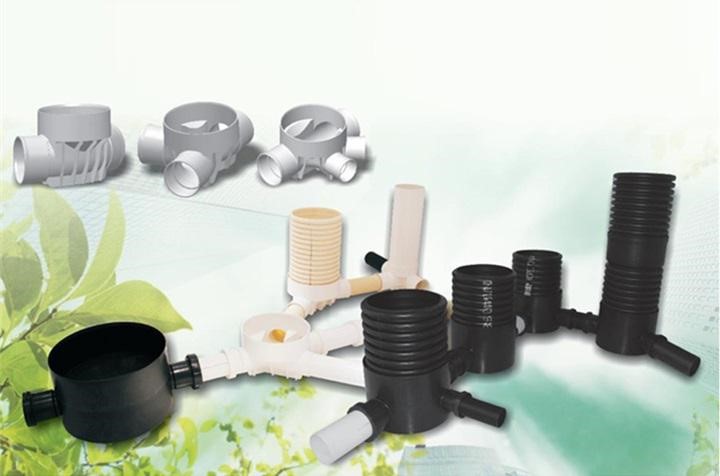
How Deep Should A Plastic Inspection Chamber be?
When it comes to drainage or any sort of underground system it’s vital to find a way to provide easy access for maintenance. And inspection
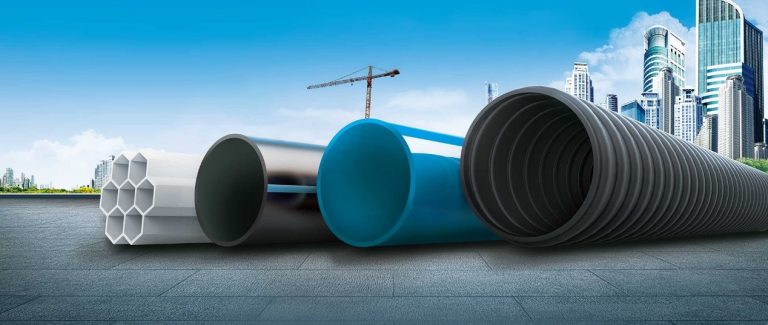
How are Plastic Pipes Manufactured
Whether they are being used for plumbing, circuits, or gas there’s no denying that pipes are one of the most useful inventions of the modern