Whether they are being used for plumbing, circuits, or gas there’s no denying that pipes are one of the most useful inventions of the modern world. But for all that we use pipes most of us don’t know too well how they are made. So today we’ll take a look at the PVC pipe manufacturing process flow and take a close look at how pipes of all kinds are made.
We’ll go over how the PVC conduit pipe manufacturing process works as well as that of PE and general plumbing pipes. So get ready and accompany us as we go over all one needs to know to truly grasp the way pipes are made and designed.
All about Plastic Pipe Manufacturing
When it comes to pipes there are no shortages of ways to manufacture them, and based on material, purpose, and company the process can change considerably. Nonetheless, we have summed it up to provide a detailed look at the 4 most common pipe manufacturing process currently in use .
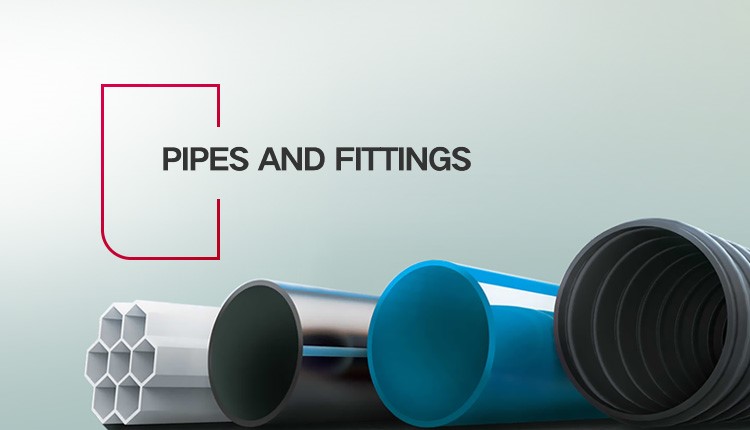
Mixing
If a natural material is used, it must first be mixed homogeneously witha color concentrate. The resin may be mixed with the color concentrate in a central blender remote from the extruder or with an individual blender mounted above the extruder hopper.
Bundling
The pipe is usually bundled before it is placed on the truck or railcar. Bundling provides ease of handling and safety during loading and unloading.
Extrusion
Extrusion takes its name from the extruder that is required for the process, and despite its apparent simplicity is one of the most reliable and involved methods to manufacture pipes. The first step is loading the raw material into the chamber of an extruder. The material in the barrel is heated up according to requirements, and can easily reach up to 200C. These high temperatures allow the material to reach the melting point at which point the material is pushed through a cavity or “die-head”.
Once the material is pushed through the extruder it gets shaped into a pipe form and keeps it once it cools down. While the basic principle is simple this method allows making pipes with low chances of irregularities or deformity. Extrusion can be used for multiple materials, but traditionally are used for a single material at a time.
Injection Moulding
At its core an injection moulding system is very similar to the process an Extruder uses. Just like in the above process the raw material is fed into an Injection Moulding machine. Inside the machine is heated through electrical heating and friction until it once again reaches melting temperature. The now melted material moves through the machine until it’s eventually poured directly into a mold. As soon as the material cools down the mould opens up and the piece is now ejected.
Injection moulding is a tried and true method that is used on countless plastic products we use on our daily lives. It allows for great fidelity and mass-production. And since moulds are highly durable too it can be affordable in the long run.
Rotational Moulding
When it comes to rotational moulding the principle behind it is once again heat, but the overall process is quite different. For this method plastic in powder or pellet form is placed on a rotating furnace. Once the plastic touches the walls of the mould it begins to melt, while the rotation makes sure it takes the shape of the mold.
Rotational Moulding is a simple and effective method however it’s used mostly for very specific parts. Rotational moulding is most often used for the manufacture of large inspection chamber or water tanks. The advantages of Rotational Moulding are that it allows to make one-piece products with little to no effort and with a simpler method than injection moulding. But usually a rotational moulding machine has only a fixed mold it can use.
Fabricated Fittings
When we talk about Fabricated Fittings we mean the smaller pieces that help connect pipes or fix a plumbing system. Compared to the other processes that focus on pipes with simple cylindrical shapes a pipe manufactured this way can have angles or even multiple entry points. Fabricated Fittings can have much more complex shapes, but require much more manual labor than any of the above-mentioned processes.
The manufacturing of pipe fittings is only inspected manually in the quality inspection step. Most production chains can be automated, for example, the cutting.
A closer look at PVC and PE Pipe Manufacturing
While the above methods we mentioned are designed to work for multiple materials and pipe designs PVC and PE bring with themselves a few unique challenges. Extrusion is by far the most common method used for the elaboration of PVC and PE pipes but thanks to the nature of the material certain modifications must be made to the extrusion system and design.
These plastics much more friction and stress to the extruder system than the alternatives. As such extruders designed for these materials not only must be built to higher standards to ensure it can withstand the working conditions. But it also must rely on a different extruder design, This twin extruder configuration decreases the stress at play while allowing the production flow to operate at normal capacity.
Sum Up
As you can see by now the manufacturing process for pipes is more elaborate than it seems at first glance, and few companies show this trait as well as LESSO does. Based in China LESSO is a company with over 30 years of experience in the pipe market and that can be easily seen in its advanced pipe manufacturing process.
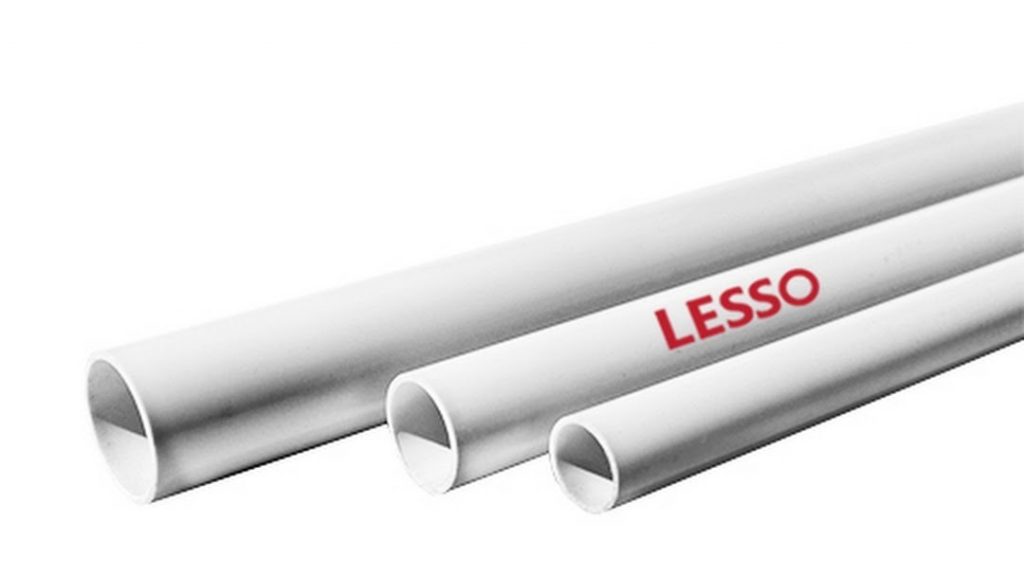
LESSO’s automated production workshop takes cost-efficiency to the next level. And if that weren’t enough on top of its state of the art manufacturing plants LESSO also counts with its own dedicated Research and Development centers to ensure their products are always at the top of the game.
Pipe manufacturing has dramatically changed and grown with the years, and companies like LESSO show how far this business still can go.
Recommend Reading
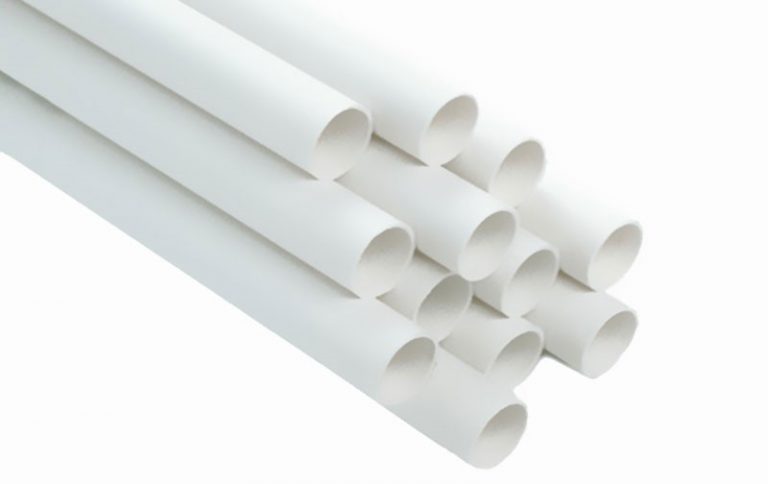
Everything You Need to Know About PVC Pipes
The third-most widely used synthetic polymer, PVC, is manufactured and used at the rate of 40 million tons a year worldwide. Its main application is
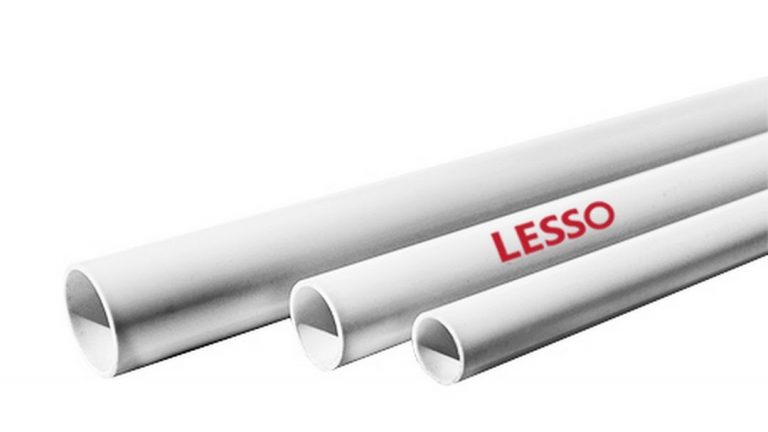
Ultimate Guide to PVC Pipe
Although working with plastic pipes is easy, you still need plastic pipe guides to get the best results. As PVC has replaced most alternatives that